BY SABITHA RADHAKRISHNA
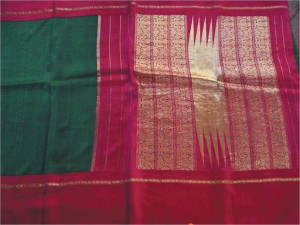
A beautiful Kancheevaram Saree!
Conjeevaram, as the British called the city now Kanchipuram, nestles on the banks of the River Vegavathi, 100 km from Chennai. It is called Silk City, being famous for the Kanchipuram pattu (silk) sarees. It is also called the city of a thousand temples and considered sacred by Buddhists, Jains and Hindus.
Patanjali’s Mahabhasya, written in the 2nd Century BCE, traces the history of Kanchipuram to centuries before the advent of the Christian era. Kanchipuram was ruled by different kings, the Pallavas in the 6-7th Century CE followed by the Cholas, the Vijayanagaram kings, the Muslims and the British.
It was during the reign of King Krishnadevaraya that major weaving communities, like the Devangas, Padmashalis and the Saligars of Andhra Pradesh, migrated to this dusty town. The locals – the Mudaliars – also became part of the weaving community.
That the finest of pure silk sarees are woven here is legendary. The main occupation of the people of the area is weaving. You will see it while walking down the streets of Kanchipuram. Everywhere you will see colourful dyed warp yarn stretched between two bamboo poles, lightly starched with rice conjee and drying in the hot sun.
* * *
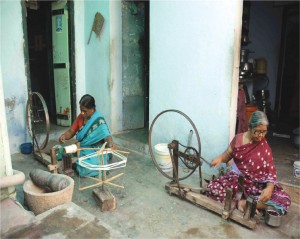
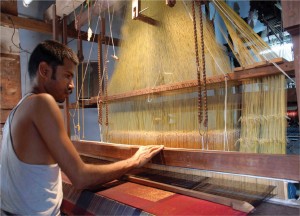
The spinners and weavers of Kanchi.
It is believed that silk weaving came here only about 150 years ago. Some say that it was 400 years ago. Before that, it was a centre only for cotton weaving. Almost every house in the city has a loom which occupies centre stage. All other activities revolve around it. For the family, the loom symbolises a comfort zone, and daily life flows around it.
Weaving is male dominated; women are engaged in ancilliary jobs like spinning, loading bobbins and stretching yarn, which is done after the household tasks are over. Children walk back and forth, questioning as they curiously touch the loom, before they too because finally engaged in the skill, knowledge of which is passed down by word of month.
Religion and weaving are closely linked. The weavers at one time looked upon their vocation with a deep sense of bhakthi. The sarees were woven primarily for the temple deities and, as most crafts do, they flourished with royal patronage. Looms came up around the temples as their needs rose. Vishnu, who was supposed to dress in a grand manner, favoured silks, so there was a proliferation of silk looms near Vishnu temples. Shiva the ascetic favoured cotton, which was why a large number of cotton looms came into operation near his temples. The weavers have always been inspired by the temples, and motifs have long been drawn from them.
Weaving dates back to the Sangam period and the weavers claim descent from Sage Markandeya, weaver of the Gods, who wove the first cloth for them from lotus fibre provided by Lord Vishnu.
A warp is about 22 metres and makes three sarees. Sale is economical only when all three sarees in the same design are sold.
* * *
According to ancient records, silk was used as early as 1725 BCE and it was supposed to have been discovered by a Chinese princess who developed a Chinese skill centred on the mulberry worm. It is also believed that a Buddhist monk brought the secret of silk and the mulberry tree to India. An old name for silk was Chinasukh.
In India the silk came from three sources, the wild tussar, eri and muga silk worms. The finest of wild silks is the textured golden muga of Assam. The Bodos of Assam are believed to have brought the art of silk reeling to the rest of India.
The Kanchipuram weavers once used only pure gold zari for the sarees, and it was considered sacrilege to use “half fine” zari. Today’s weavers, dictated by demands of a non-traditional market, use whatever simulates the same effect. The gold zari was supplied by the Patnoolkarar community that lived in the temple area in the centre of Madurai. This community of gold thread weavers were traditionally from Saurashtra. They first migrated to Maharashtra and then to Vijayanagar keeping to themselves the secret of how to make zari thread. Gold is 0.6% and silver 57% in the zari used.
Today, the real zari comes from Surat and the cost is phenomenal about – Rs 7500 a ‘mark’ of 3,000 metres. The Tamil Nadu Government has set up a centre for supplying gold zari, but the weavers say it is not satisfactory and prefer to take their supply from Surat. The pure zari consists of a silken red thread covered by a flattened silver thread which is later dipped into molten 24-carat gold for the ultimate finish. This why many of us at some time or the other, melt old sarees which are torn and out of vogue to obtain pure silver. I appeal to all of you not to do this, but bring such sarees to the notice of textile activists who could revive these old classics and donate them to some textile museum.
What sets the Kanchipuram saree, a gem among Indian sarees, apart from others, making it a prestigious brand? The unique characteristic of a the legendary Kanchipuram saree in resplendent colours, with contrasting borders and pallus. is the use of good quality, three-ply twisted silk yarn and pure zari (when used),which guarantees its richness and texture.
Originally the sarees were worked with three shuttles in order to facilitate the korvai for which it is so famous. The two shuttles at the side carry the colours of the border whose thread matches the border warp exactly. The third and middle shuttle carries the thread, which is dyed for the main body of the saree. By throwing the shuttles back and forth, the saree is woven continuously, interlocking the border as it is being woven. The joinery is done on the looms itself, sometimes with little temple spires to cover the defects of interweaving. The weaving with adai, which is defunct today, is replaced by jacquard weaving and punched cards. In korvai weaving, the borders are solid, usually contrasted with the main body of the saree. The main feature of the Kancheepuram saree is the korvai technique where the border and pallu is each a solid colour,and where the weft does not enter the warp thread in both these areas. The glowing colours of these sarees are attributed to the washing done in the Palar river which had certain minerals which enhanced the colours.
The pallu of the saree, which will ultimately be of solid colour to match the border, is woven by cutting the warp threads, and adding a new warp by connecting the new set of warp threads with the original warp of the body. The main body warp and the warp of the pallu are woven with the weft threads of the pallu for a few inches before cutting off the warp of the main body. This technique, called petni, is the same as what is employed to weave Gadwal sarees. When the saree is more special, an overweave in weft is incorporated in the form of butti-s all over the body and sometimes as an extra weave in the border and pallu.
Because it is so complicated, the kattu saayam method is employed. In this process, a single warp is dyed with two or more coloured dyes in order to have different body and pallu hues. This is generally achieved by dyeing one saree warp length [both body and pallu portion] with body colour first, stripping the pallu colour by means of bleaching, which is a reduction process and, finally, dyeing the pallu portion with a different colour.
The main disadvantage associated with this tie & dye process is that repeat dyeing of warp and stripping/ bleaching of the pallu portion results in poor tenacity properties reducing the life of the saree and its durability, particularly of the pallu portion.
Initially, a design was drawn using a tracing paper and plotted on to a graph sheet. The design was then punched on to a cardboard sheet, a laborious process as it is manually executed. The prepared punch card or the design pattern became part of the set-up loom and handed over to the weaver for the saree to be woven.
Today, people depend on computers for design, as weavers trained in the 1970s were getting too old to carry out this work. This had led to automation of the process. The image of the design is scanned and then traced and filled with bitmaps. The image is transferred on to the punching card software and then placed in the jacquard machine by the weaver to facilitate the weaving process.
Today only two weavers sit at the loom. A mechanised shuttle was invented by Bhanumurthi, Master Weaver, for which he received the National Award.
The whole process used to take around five hours. It is not easy to locate a cotton korvai saree. The wages are higher for silks. For a special design saree it is about Rs. 5,000 per saree, as against Rs. 1000 for a cotton, so not many weavers agree to sit at a cotton weaving loom. It would take a month to weave a traditional Kancheepuram silk saree.
* * *
The scenario in the famed city is changed today. Poor working conditions, renumeration not commensurate with the long hours of labour, and a changing market, have damaged the psyche of the traditional weaver. Perplexed by the new demands of a contemporary market, he is orphaned, and feels that he is doomed to lead a life of utter poverty. Where the weavers’ own children could help in loom work, the Child Labour Act has cut the flow of production. The parents encourage their children to leave the warp and weft and look for higher paid jobs. Multi-national companies pick up young men and women to work in their factories. To the young it is prestigious to hold a “factory job”, even if it entails sweeping, for it fetches them a regular income rather than perspire over a loom. As a result, traditional Kancheepuram weavers are diminishing in number alarmingly and before you know it this gem of a saree will become a museum piece.
Kancheepuram is an example of the malaise that is spreading to the rest of the weaving centres in the country. Shops today flaunt poor imitations of the original as Kanchi silks, and these are bought by gullible customers. A genuine Kanchi silk saree will not weigh less than 650 gms, will be woven with two or three ply yarn, and the zari used would be real.
Are we still rooted in a traditional aesthetic or do we move forward to keep handlooms in the forefront forever? Textile experts should research and create handlooms of the best quality and consider innovations to suit the contemporary market as part of the process of change. You need to remember that the handloom weavers are national treasures and you need to give them a special niche.
Credit: http://www.madrasmusings.com/archives/